La compaction des enrobés
Une science à géométrie variable
« Le passage répété des véhicules et la présence de véhicules lourds sont associés à la présence d’ornières dans le revêtement de la chaussée. Parce qu’elles se forment sous les traces des roues des véhicules, elles peuvent causer des accumulations d’eau, des risques d’aquaplanage, des problèmes de sécurité pour les usagers et un réel inconfort de roulement pouvant ralentir la circulation », explique Guy Tremblay, directeur du laboratoire des chaussées au Ministère des Transports, de la Mobilité durable et de l’Électrification des transports. Les donneurs d’ouvrages cherchent à éliminer leur présence sur le réseau routier. « Or, en cas d’ornière, le premier critère à prendre en compte est la structure même du revêtement et les conditions dans lesquelles il a été posé. »
par Michel Joanny-Furtin
Selon le Guide technique sur la mise en place des enrobés bitumineux, le compactage d’un enrobé vise à densifier le matériau au pourcentage de vides optimal et à sceller la surface en la rendant uniforme, afin d’obtenir les propriétés mécaniques désirées pour assurer la durabilité du revêtement et des caractéristiques d’adhérence compatibles avec la sécurité des usagers de la route. Car les problèmes de compaction ont des impacts sur la durée de vie de l’ouvrage réalisé.
De nombreuses variables…
« La norme 4202 encadre la formulation des enrobés utilisés. En poids, les enrobés sont généralement constitués d’environ 95 % de granulats et de 5 % de bitume. Le Ministère répertorie à ce jour 9 mélanges, lesquels couvrent environ 98 % des usages requis sur le réseau routier du
Ministère », rappelle Michel Paradis, ingénieur responsable du secteur enrobés. « Un «orniéreur de laboratoire» nous permet de prédire en laboratoire le comportement d’un enrobé sur la chaussée pour la résistance à l’orniérage après le compactage, en plus de rechercher de nouvelles approches pour affiner la compaction. Si l’enrobé répond aux exigences de formulation du ministère, et qu’on observe malgré tout des dégradations prématurées après 3 ou 4 ans, nous devrons vérifier si les mélanges sont bien formulés, bien produits en centrale d’enrobage ou le résultat d’une pose déficiente en chantier (apparition de divers phénomènes tels l’orniérage de post-compaction). »
Lorsqu’un enrobé mis en place à chaud est compacté correctement, le bitume et la fraction fine du mélange forment une matrice dans laquelle les gros granulats sont maintenus. L’enrobé doit résister aux pressions sans se déplacer verticalement (post-compactage). C’est le compactage idéal.
« Les enrobés ne se comportent pas tous de la même manière durant le compactage, selon des conditions parfois idéales ou parfois limites», note Michel Paradis. « Cette problématique de la compaction des enrobés est une préoccupation importante pour les donneurs d’ouvrage, les ingénieurs, les entrepreneurs, qui doivent élaborer leurs stratégies de revêtement selon plusieurs éléments comme la granularité, la forme des granulats, la classe de bitume, la teneur en bitume de l’enrobé, la température ambiante, celle de l’enrobé et celle de la surface à recouvrir, la teneur en eau des granulats, l’épaisseur de la mise en place, le confinement du mélange et les conditions de la fondation granulaire. Le comportement au compactage est également influencé par les conditions climatiques, le facteur temps à la livraison comme à la pose de l’enrobé… et l’état de la machinerie utilisée par l’entrepreneur ! »
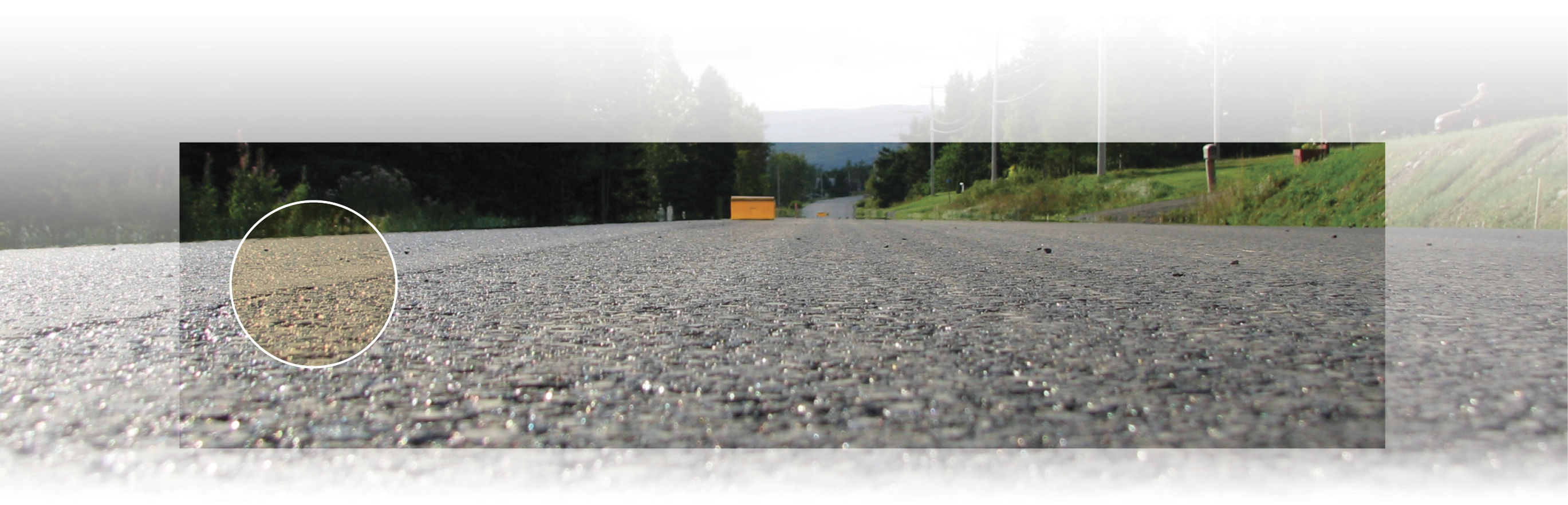
La part de l’entrepreneur
« La performance de l’équipement de compactage doit effectivement être prise aussi en considération », confirme Benoit Pichette, ingénieur responsable du secteur surveillance. « Il faut effectuer fréquemment des planches d’essais pour déterminer un bon plan de compactage. L’utilisation d’un rouleau compacteur approprié optimisera le nombre de passes requises et favorisera une compacité uniforme conduisant à un revêtement plus performant. »
Ainsi, à partir des variables énoncées, un logiciel permet de calculer le temps nécessaire des opérations afin de limiter les écarts de température et réaliser la compaction idéale. Dans le même ordre d’idée, l’évolution des nouvelles technologies favorise la conception d’enrobés plus performants. Des appareillages électroniques (nucléodensimètre, tomodensimètre, caméra infrarouge pour relevés de thermographie, etc.), permettent les contrôles les plus immédiats avant, pendant et après la pose de l’enrobé et complètent des approches plus classiques comme la règle de trois mètres, le carottage ou… le thermomètre à tige !
Un processus précis
La mise en place des enrobés bitumineux doit se faire en se fixant comme objectif de réduire au minimum les variations de température à l’arrière du finisseur. Par la suite, le mélange est compacté rapidement afin de s’assurer que le bitume ait la viscosité idéale et uniforme pour faciliter le travail », rappelle Benoit Pichette. « Les rouleaux compacteurs doivent commencer le compactage le plus tôt possible après la mise en place de l’enrobé par le finisseur. « Le compactage se fait généralement en trois étapes: le compactage initial, le compactage intermédiaire et le compactage final. Le compactage initial suit directement le finisseur et doit s’effectuer à la température uniforme de l’enrobé la plus élevée possible, soit celle qui supportera le poids du rouleau sans causer des déplacements excessifs de la surface. Les équipes disposent d’une fenêtre réduite de temps pour le faire adéquatement. En effet, à mesure que la surface refroidit, la viscosité du bitume augmente et il devient plus difficile d’obtenir une surface suffisamment compactée et imperméable. »
« Le compactage intermédiaire vient ensuite pour assurer une bonne imperméabilité du revêtement », poursuit-il. « Le compactage final sert à effacer les traces laissées par le compactage précédent. Mais il faut prendre garde à ne pas “surcompacter” le revêtement, car cela peut conduire à un mauvais fini de la surface. Divers types de rouleaux sont utilisés pour la réalisation du compactage. Si la compacité minimale requise n’est pas obtenue à la fin du processus de compactage, la circulation pourra causer des déformations et de l’orniérage sur le revêtement. »
Tout est donc une question d’équilibre entre les interventions humaines, les températures, le site et son climat, la cadence de travail et le bon état des équipements, et surtout une bonne préparation et une excellente coordination entre les intervenants pour déterminer le meilleur scénario de compactage. •